Product Description
Filter presses are widely used to separate suspended solids from liquids in various industrial processes.
Main Components of a Filter Press:
-
1. Frame – The main supporting structure
-
2. Filter Plates – Chambers where the filtration occurs
-
3. Manifold System – Includes piping and valves for slurry distribution and filtrate discharge
-
4. Filter Cloth – The key filtering medium that retains solids
Compared to other dewatering technologies, filter presses offer the driest cake and the clearest filtrate. Optimal performance depends on proper selection of filter cloths, plate design, pumps, and accessories such as precoating, cake washing, and squeezing.
Holly Filter Press models include: Fast-opening filter press; High-pressure filter press; Frame filter press; Membrane filter press.
Multiple types of filter cloth are available: Multifilament polypropylene; Mono/multifilament polypropylene; Monofilament polypropylene; Fancy twill weave filter cloth.
These combinations allow customization for different sludge types and treatment goals.
Working Principle
During the filtration cycle, slurry is pumped into the press and evenly distributed into each chamber formed by the filter plates. Solids accumulate on the filter cloth, forming a cake, while the filtrate (clean water) exits through the plate outlets.
As pressure builds inside the press, the chambers gradually fill with solids. Once full, the plates are opened, and the formed cakes are discharged, completing the cycle.
This pressure-driven filtration method is highly effective for achieving low moisture content in sludge.
Key Features
-
✅ Simple structure with linear design, easy to install and maintain
-
✅ Uses high-quality, internationally recognized components for pneumatic, electrical, and control systems
-
✅ High-pressure dual-cylinder system ensures secure plate closing and efficient operation
-
✅ High level of automation and environmental protection
-
✅ Can be connected directly to filling machines via air conveyors for streamlined processing
Typical Applications
The filter press is widely used in various industries for sludge dewatering and solid-liquid separation. It is especially effective in treating high-moisture or high-viscosity sludge.
The filter press is often used in the following sectors:
Technical Parameters
Choose the right model based on your required filtration area, capacity, and installation space.
(See the table below for detailed specifications.)
Model | Filter Area(²) | Filter Chamber Volume(L) | Capacity(t/h) | Weight(kg) | Dimension(mm) |
HL50 | 50 | 748 | 1-1.5 | 3456 | 4110*1400*1230 |
HL80 | 80 | 1210 | 1-2 | 5082 | 5120*1500*1400 |
HL100 | 100 | 1475 | 2-4 | 6628 | 5020*1800*1600 |
HL150 | 150 | 2063 | 3-5 | 10455 | 5990*1800*1600 |
HL200 | 200 | 2896 | 4-5 | 13504 | 7360*1800*1600 |
HL250 | 250 | 3650 | 6-8 | 16227 | 8600*1800*1600 |
Packing & Global Delivery
Holly Technology ensures secure and professional packaging of every filter press for safe transportation.
With a proven track record of global shipments, our equipment is trusted by clients in over 80 countries.
Whether by sea, air, or land, we guarantee timely delivery and intact arrival.
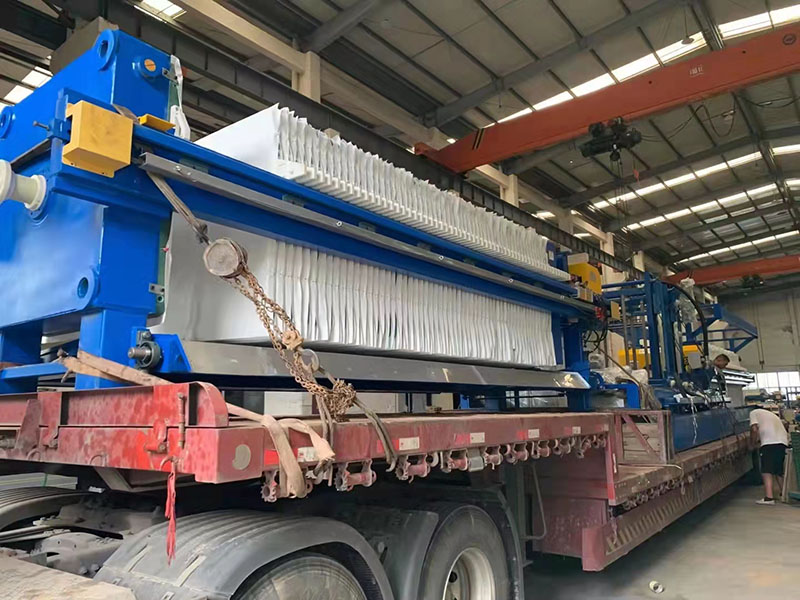
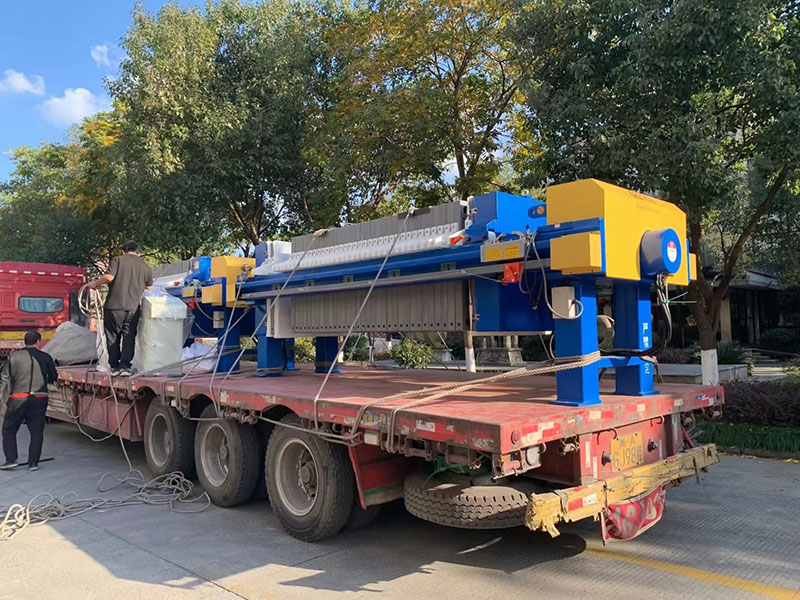
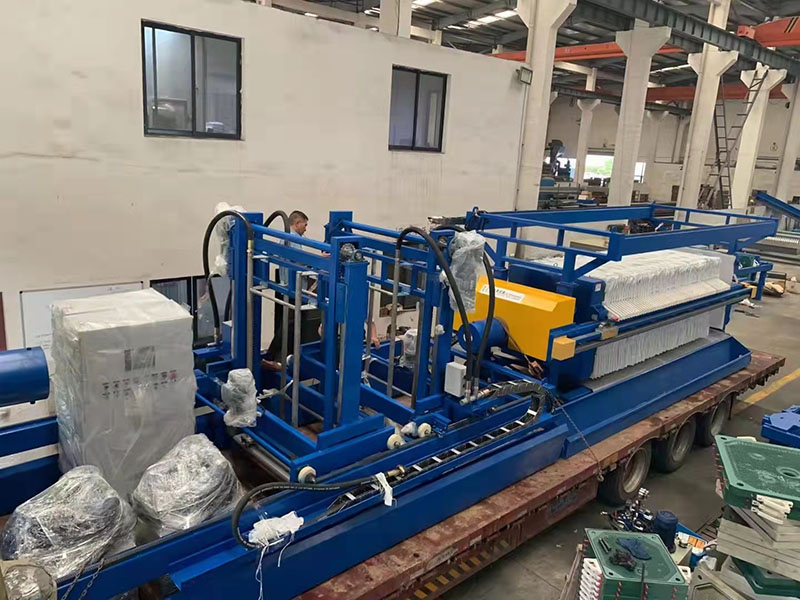
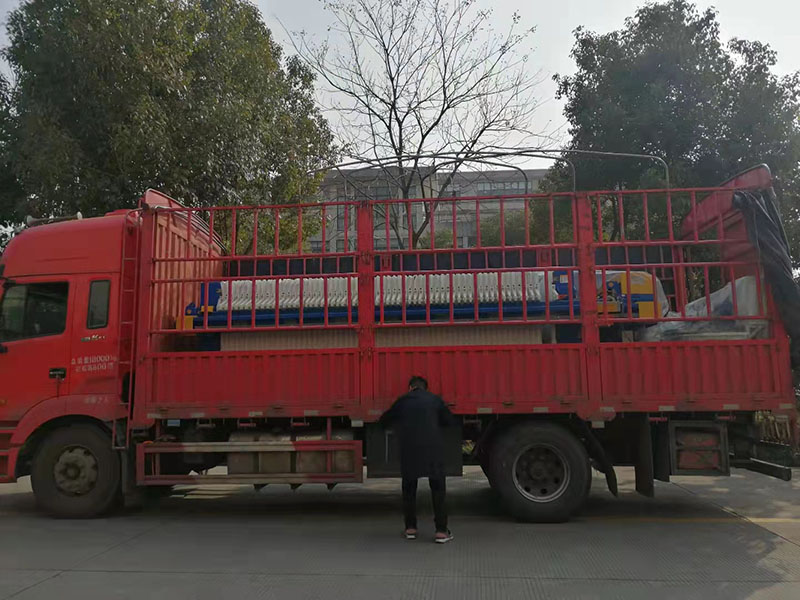